Solid-propellant rocket motor test stand (BEAP)
Among the many facilities of Europe's spaceport, the BEAP is one of a kind. It was specially designed for the development and qualification of the solid propellant engines that power the European launch vehicles.
Key equipment
Designed and operated by the CNES since 1991, the purpose of this test bench is to qualify the solid propellant engines being developed for future launch vehicles and contribute to technology monitoring programmes.
The BEAP was first used to test the solid rocket boosters used by Ariane 5 and Vega, then their upgrades for Ariane 6 and Vega-C and even the future Vega-E, under real conditions.
This ensures that these critical components are operating correctly before they are used in flight. These tests are essential for validating booster design, the materials used and production techniques, guaranteeing booster performance and reliability and contributing to the continuous improvement of solid propellant technologies on a European scale.
Test stand infrastructure
The BEAP is composed of a test area and a dedicated control station.
The test stand itself is composed of a 50-metre-tall metal tower, which has the booster for fire testing installed on the front of it. The tower stands on a concrete platform overlooking a huge flame trench cut into the granite. Measuring 200 metres long, 35 metres wide and 60 metres deep, with an impressive volume of 250,000 cubic metres, this flame trench is designed to channel the combustion gases produced during the launches.
The BEAP is linked by rail to the booster integration building (BIP), where both the qualification specimens to be tested and all the solid propellant engines used for the launches are prepared.
Approximately one km from the BEAP is the remote control station, located in a sealed bunker to provide safe shelter for the teams. It mainly comprises offices and a command-control room, with four control desks to remotely control fire testing.
A focal point for technology… and safety
The BEAP is equipped with mechanical devices and command-control systems that enable the testing phases to be managed and monitored completely safely.
To accurately quantify engine performance, the BEAP is equipped with a highly sophisticated thrust measurement system (TMS). Weighing 20 tonnes and standing 40 metres tall, the TMS holds the booster in place during the test. It measures its thrust, dampens the shock from the ignition while providing a certain degree of freedom so that it takes place under flight-representative conditions, and weighs the test specimen after firing.
From the control room, the data acquisition system records all the measurements collected by the sensors installed on the booster and the test bench itself. A sophisticated command-control system orchestrates the entire test, including checking the engine nozzle and controlling the actuators that direct the nozzle.
During testing, the booster is held firmly in place by rings and a safety cable to prevent it from lifting off. However, in the highly unlikely event that the system should fail, the test bench is equipped with anti-flight 'knives': articulated arms configured to strike the engine casing and destroy it on the spot.
Fluid systems that supply nitrogen, helium, hydraulic fluids and water are also included for testing and cooling purposes.
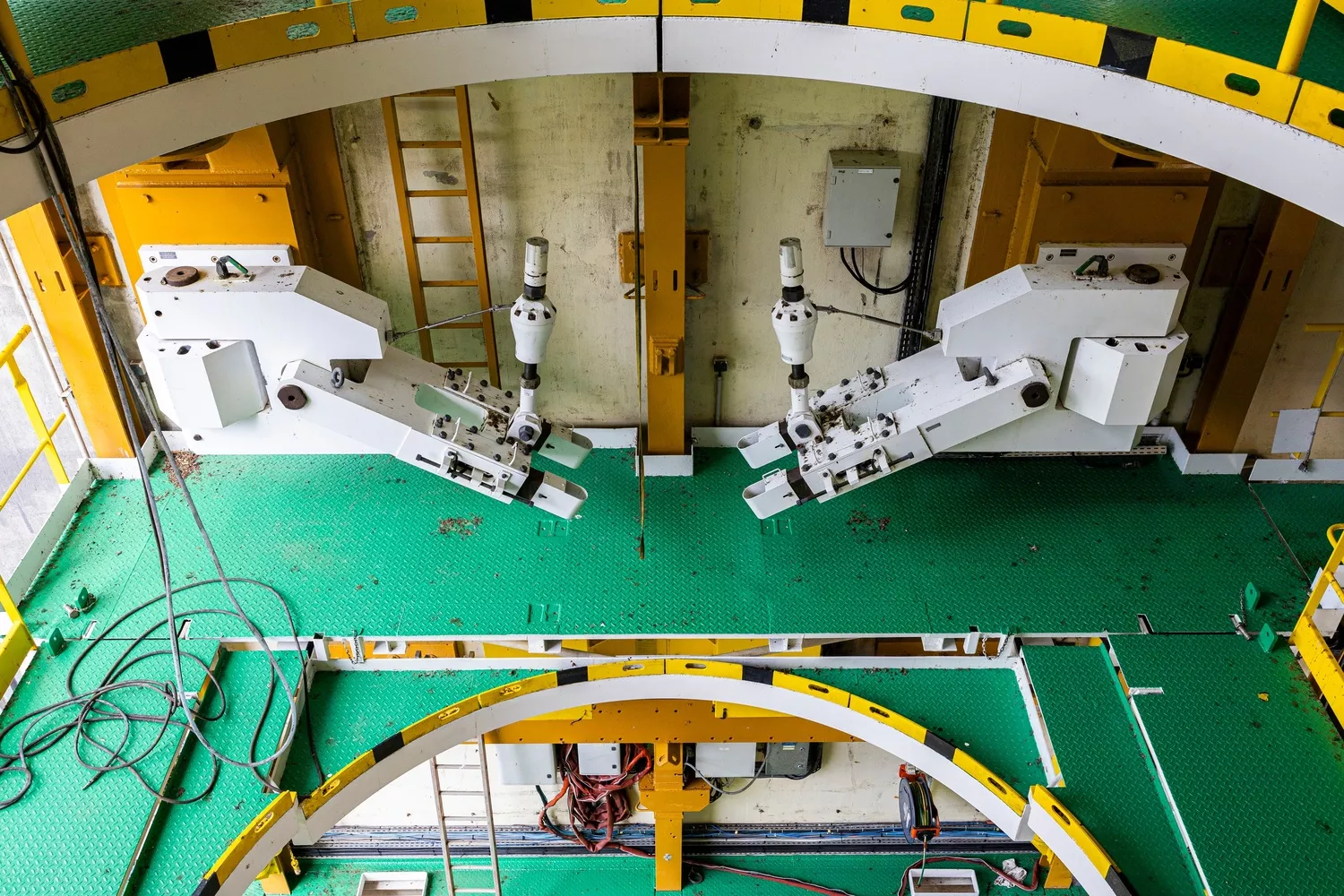
The anti-flight 'knives' are jointed arms that penetrate the specimen to ensure its destruction if an unanticipated takeoff occurs.
How fire testing works
A BEAP test campaign may appear similar in many ways to a launch campaign, but it has its own specific features.
1. First of all, the BEAP needs to be reactivated, i.e., all the systems need to be switched back on and checked after their mothballing phase, which can last several years between two tests.
At the same time, the flame trench, which is usually filled with rainwater, is emptied. For environmental reasons, it must be completely drained before testing to avoid contaminating the water, which would subsequently be released back into the environment. Complete emptying takes an average of three months.
2. During this time, Europropulsion prepares and assembles the solid propellant rocket motor in the Booster Integration Building (BIP). It is equipped with around 600 sensors and mechanical devices enabling it to interface with the test bench. It is then transported from the BIP to the BEAP using a special pallet on tracks.
3. The actual test campaign is carried out by the French Space Agency: receiving and fitting out the booster at the BEAP, connecting it to the measurement equipment, performing control tests and installing safety systems and heat protection. Blank firing is carried out on D-1.
The team, coordinated by a test manager, is made up of around 15 people. Just like for a launch campaign, it uses the spaceport's shared cross-cutting resources (air conditioning, power, fire detection, water network, video optics, etc.) and activates the Safety, Weather and Security services.
4. After firing, which can take more than two minutes for an engine like the P160C, which contains 160 tonnes of powder, the data collected is meticulously analysed to check its performance and compare it with forecasts.
A crucial stage immediately after firing consists of cooling the systems using nitrogen, in order to stop the combustion of the test model components as quickly as possible and thus obtain the most reliable observations.
5. The campaign ends with the dismantling of the measurement equipment and the mothballing of the site... until the next test.
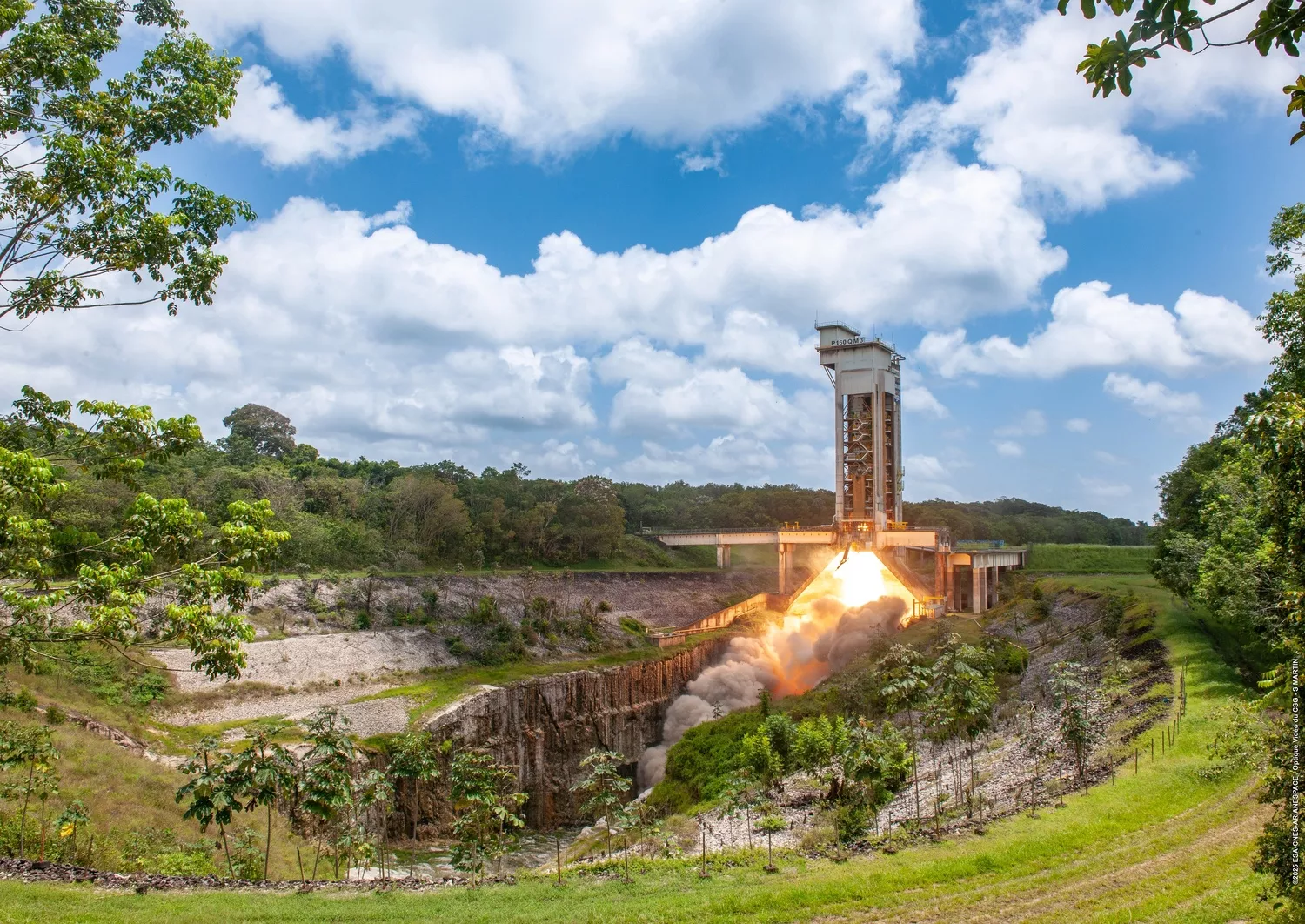
The test firing of the P160C, the future engine for the Ariane 6 and Vega C launch vehicles, was successfully conducted on April 24, 2025.
Since it was commissioned in the early 1990s, the BEAP has undergone a number of updates to adapt it to the development of ever larger and more sophisticated solid rocket boosters.
The first fire testing, B1, was carried out on 16 February 1993, helping qualify the engines of the Ariane 5 rocket. Since then, the BEAP has been used for 19 significant fire tests, stemming from various solid propellant engine development programmes.
The latest, on 24 April 2025, was the P160C engine intended for an upgraded version of the Ariane 6 launch vehicle, known as "Block 2", as well as for Vega-C and its successor, Vega-E.